he perfect storm is a popular expression coming from a novel
written in 1997. It is when certain weather occurrences, when separate are no
problem, come together by chance and create a catastrophe. While Hurricane
Isabel may not have been the perfect storm, it was the perfect opening into the
marine construction field for Brian Fletcher with Delta Marine Construction.
For those of us living on the Northern Neck or Middle Peninsula, the mere mention of Hurricane Isabel sends shudders down our spine and flashbacks to ruined shorelines, piers, and even homes. This was a time when many of the quaint river cottages, built decades before, were flattened; now in their place we find grandiose river villas. Walking on a pier that had been damaged felt much like walking the tracks of a roller coaster.
When all of this hit, Brian Fletcher was running a farm in Deltaville. One of his buddies that he had known from fishing owned Deltaville Marina and Deltaville Boatyard. To say that Hurricane Isabel had hit the marina and boatyard was putting it mildly. His friend recruited Brian to help repair the destroyed property and from there Delta Marine Construction was born.
Before Brian moved to Deltaville in 2001 from Georgia, his background was in agriculture. Although his past profession was not marine construction, he has been installing piers and seawalls on fresh water lakes in Georgia for many years. His very first experience with marine construction was nearly 18 years ago.
When Brian began working with the owner of Deltaville Marina and Deltaville Boatyard they were in the process of constructing a barge to drive pilings. Brian joined up with him and together they completed the barge construction and became partners at Delta Marine Construction. This became the perfect partnership; Deltaville Marina had the equipment and Brian had the manpower.
Deltaville Marina and Deltaville Boatyard were among the first clients of Delta Marine Construction. Once that work was completed, Brian and his partner began repairing the damage Hurricane Isabel had done to the area’s residential piers, docks, seawalls, and
other marine architecture. Many times this involved replacing the original structures entirely with new structures that would withstand future storms or hurricanes. After two years, Brian bought out his partner’s share of the business and became the sole owner of Delta Marine Construction.
Delta Marine Construction specializes in projects suitable for residential properties and small- to mid-range commercial projects.
In the years since Brian took over as the sole owner of Delta Marine Construction the business has really grown. They have gone from having one barge for driving pilings to five, three of which have the capacity to be taken apart and driven across the state or country on a trailer. This is particularly helpful when doing jobs on lakes or ponds. A little over a year ago, they also opened another office in Fairfax County.
Delta Marine Construction specializes in projects suitable for
residential properties and small to midrange commercial projects.
Their quality construction and dedication to innovation has
made them one of the leaders in marine construction in Virginia’s Bay region.
It is Delta Marine Construction’s dedication to quality and design innovation that makes their work stand out. Part of what plays in to their quality construction is that they refuse to use pilings or poles with less than an eight inch tip. The tip of the piling is the skinniest point at the very top, so eight inches at the tip will lead to a wider foundation at the bottom. Pilings of this size are beneficial because they are better able to weather storms. Large pilings are also less affected by ship boring worms, which dig holes into underwater wood and can reduce the integrity of the wood.
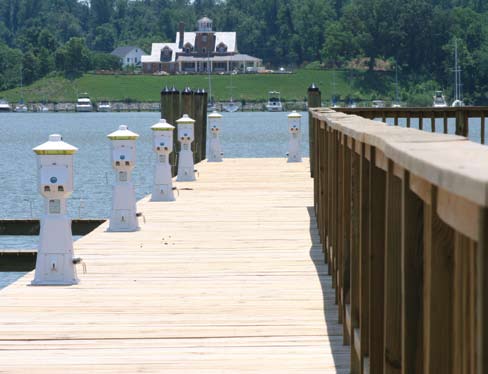
|